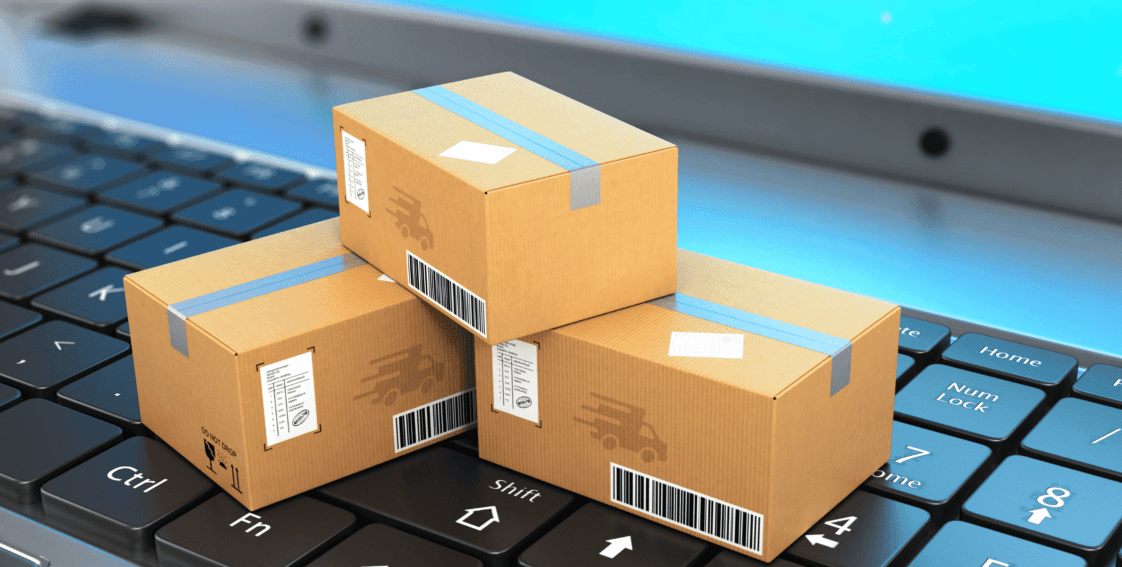
Set the Alarm
For every project, the Electronics Manufacturing Service Provider (EMS Provider) strives to enable partners on-time delivery (OTD) services. The initial conversations between provider and partner are necessary to establish the proper steps to success. Overall, these conversations develop the needs of the project at hand and indicate priorities for the build. Delivering on-time services is critical for customer service and proper project completion.
Setting the alarm before bed takes careful consideration. How many times will you press snooze? When will you eat breakfast? How long does it take for you to do your signature hair-do? Similarly, setting the timer for a project takes thoughtful deliberation. Key factors include expertise, staffing, technology standards, and transparency on the supplier side.
Expertise
Firstly, an experienced supplier should effectively build their services to support their customers’ needs. In practice, these solutions extend past assembly to industry knowledge. To strive for on-time delivery, a supplier should:
-
- Evaluate Obsolete Parts
- Check End-of-Life Parts
- Assess Lead Times
- Review Applications for Components
- Provide Substitutions/Alternatives
Overall, experience in the industry allows certain suppliers the inner know-how to navigate component acquisition and potential production time.
Staffing
Knowledge alone cannot prevent sleeping through the alarm. Proper employee training in the correct positions is crucial to waking up refreshed and ready to go!
If a company is understaffed and overworked, the delivery goal will be much harder to reach. Regular assessments of business practices, managerial roles, and training practices must occur to counter this problem. Establishing effective training procedures and recognition allows the right employee to fill a vital position.
After all, companies operating with the best person for each task are guaranteed to create an efficient production process with fewer snooze button hits.
Technology Standards
Coupled with the right team, establishing top-notch technology and machinery streamlines production processes wherever possible. For instance, Surface-Mount Technology (SMT) machines perform PCB Assembly tasks such as component placement more quickly than complete manual assembly.
For companies searching for a supplier, it is essential to visit the facility or receive a list of the machinery they can equip for your project. Furthermore, if your project is for a growing industry, such as Electric Vehicles, evaluating the machinery for its longevity eliminates future supplier changes and production delays.
Transparency
On the whole, constant updates reassure the customer that the supplier has their best interest in mind. This honest feedback incorporates positive and negative situations involved with a project’s progress. For example, suppose a supplier becomes aware of a pending issue that will delay the procurement of specific components if a different course is not taken. In that case, they should immediately notify the customer to plan an alternate solution and maintain trust.
These constant discussions could generate new ideas to continue the path to on-time delivery, even when blocks seemingly get in the way.
Avoid Hitting the Snooze
In summary, with a customer’s keen attention to supplier services and the supplier’s constant assessment of their capabilities, partners can achieve on-time delivery even in times of supply chain turmoil. The final piece of advice is for both parties to have realistic goals. Especially during component shortages, everyone should review the path to production with the goal of re-defining order periods and lead times. With all of these tips in mind, springing out of bed at the first alarm should come easily!